Температура размягчения динасовых кирпичей выше, чем у шамоных кирпичей и кирпичей с высоким содержанием глинозема, которая может достигать 1640 ~ 1670 ℃. Стойкость к кислотной коррозии кремнеземных кирпичей высока. Основным компонентом является sio2, который отличается от высокоглиноземистого кирпича. Основным компонентом высокоглиноземистого кирпича является глинозем, который обладает сильной кислотостойкостью и стойкостью к щелочам. Динасовый кирпич – огнеупорный кирпич, который часто используется в коксовых печах. Сегодня мы рассмотрим некоторые характеристики динасового кирпича для коксовых печей.
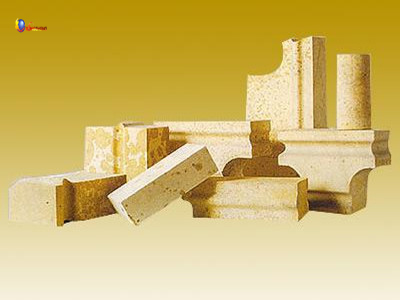
Динасовые изделия для коксовых печей
Характеристики динасового кирпича для коксовой печи:
1 Химический состав динасового кирпича варьируется в зависимости от кремнеземного сырья. Как правило, содержание SiO2 составляет 93–98%, а других примесей, таких как SiO2, Fe2O3, CaO и т. Д., Составляет 2,0–7,0%.
2 В минеральном составе динасового кирпича обычные динасовые кирпичи в основном состоят из тридимита, составляющего от 30% до 70%; динасовые кирпичи с высоким содержанием кремния и высокой плотности состоят в основном из кристобалита, составляющего от 20% до 80%; остаточный кварц и не хрустальное кварцевое стекло содержится в небольшом количестве в динасовых кирпичах.
3 Огнеупорность динасового кирпича в основном зависит от содержания SiO2, содержание примесей и его свойств. Чем выше содержание SiO2, тем меньше содержание примесей, и чем ближе ее огнеупорность к точке плавления SiO2, а, наоборот, чем ниже огнеупорность, огнеупорность динасового кирпича, как правило, 1690 ~ 1730 ℃.
4 Температура размягчения динасового кирпича относительно высока, около 1650 ° C, поскольку кристаллическая сетчатая структура тридимита играет каркасную роль в дмнасовом кирпиче. Хотя некоторые примеси имеют низкую температуру плавления, так как структура имеет определенную несущую способность, его температура размягчения нагрузки близка к его огнеупорности, которая является существенной особенностью силикатного кирпича.
5 Шлакостойкость кварцевого кирпича. Основной химический состав динасового кирпича – это типичный кислый оксид SiO2, который определяет сильную стойкость к кислому шлаку. В то же время Fe2O3, CaO и SiO2 могут образовывать новые соединения, поэтому кремниевый кирпич все еще имеет определенную стойкость к Fe2O3 и CaO в шлаке, которые являются щелочными оксидами.
6 Истинная плотность динасового кирпича отражает степень превращения кварца в силикатном кирпиче, так что можно судить о минеральном составе. Чем ниже истинная плотность, тем лучше. Чем ниже истинная плотность, это означает, что кварц хорошо трансформируется и остаточное расширение, возникающее при фактическом использовании, меньше.
7 Пористость динасового кирпича показывает степень плотности динасового кирпича. Чем меньше пористость, тем плотнее структура. Кажущаяся пористость силикатного кирпича обычно составляет 21% ~ 25%. Размер пористости, помимо сырья, в основном зависит от условий его процесса.
8 Прочность кварцевого кирпича на сжатие при комнатной температуре в основном используется для определения качества структуры силикатного кирпича. Прочность на сжатие при комнатной температуре часто тесно связана с пористостью и истинной плотностью. В то же время это также зависит от природы сырья, условий процесса и так далее. Прочность на сжатие кварцевого кирпича при нормальной температуре обычно составляет 19,6 ~ 29,4 МПа.
Кирпичи динасовые используются в основном для изготовления перегородок камеры карбонизации и камеры сгорания коксовых печей, регенератора и шлаковой камеры сталеплавильных мартеновских печей, пропиточных печей, огнеупорных материалов для стекловаренных печей и сводов керамического обжига. печи и другие несущие части. Это хороший огнеупорный кирпич.Если вам нужны динасовые или другие огнеупорные кирпичи и литейные изделия, вы можете связаться с нами.