Коксовая печь – это печь, в которой уголь используется для получения кокса. Это основный термический агрегат для коксования. Коксовая печь состоит из камеры, куда загружается угольная шихта, обогревательного простенка, состоящего из системы отопительных каналов, в которых горящие газы обогревают стены коксовой камеры, системы газораспределительных и воздухоподводящих каналов, подающих газ и воздух для отопления печей, регенераторов для нагрева воздуха (бедного газа) и отвода продуктов сгорания, соответствующей арматуры и механизмов. В соответствии с различными условиями работы каждой части коксовой печи, в качестве огнеупорных материалов выбираются динасовые кирпичи, полусиликатные кирпичи, шамотные кирпичи, высокоглиноземистые теплоизоляционные кирпичи, силлиманитные кирпичи, красные кирпичи, огнеупорные бетонные смеси и другие виды огнеупор.
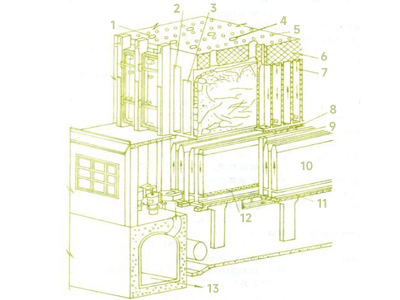
1 – газоотводящие люки, 2 – камера коксования, 3 – камера сгорания, 4 – загрузовые люки, 5 – смотровая шахточка, 6 – свод комеры, 7 – вертикал, 8 – косые ходы, 9 – газопровод, 10 – регенератор, 11 – подовый канал, 12 – насадка, 13 – борова
Полусиликатные кирпичи – это алюмосиликатные огнеупорные изделия с содержанием SiO2 более 65 %, обычно изготавливаемые из кварцевого песка, содержащего огнеупорную глину, хлорита и огнеупорной глины или каолина. Полусиликатный кирпич не сильно расширяется при нагревании, и это небольшое расширение лишь помогает улучшить целостность кладки. Полусиликатный кирпич поможет ослабить эрозионное воздействие шлака на кладку. Когда высокотемпературный шлак вступает в контакт с поверхностью кирпича, на поверхности кирпича образуется слой вязкого глазуреподобного материала, который может препятствовать дальнейшему проникновению раствора внутрь кирпича, образуя защитный слой, тем самым повышая эрозионную стойкость кирпича. Полусиликатные кирпичи используются в средней и нижней части теплоаккумулирующего помещения коксовой печи, и цель применения полусиликатных кирпичей – обеспечить герметичность кладки и предотвратить эрозию кладки кислотными веществами (при нагревании доменным газом).
Насадочный кирпич для регенераторов коксовой печи обычно представляет собой шамотный кирпич. Некоторые производители в целях снижения стоимости некоторых видов сырья с высоким содержанием Al2O3 для замены основного сырья шамотного кирпича – кремневка, в результате чего в коксовой печи, отапливаемой доменным газом, верхние насадочные кирпичи в регенераторном камере в восстановительной атмосфере подвергаются эрозии кислыми газами, что приводит к явлению плавления и вспучивания. Позже было введено требование к содержанию Al2O3 в четырехслойных насадочных кирпичах в верхней части регенераторов, которые стали называться насадочными кирпичами с низким содержанием алюминия. Требования к содержанию Al2O3 от 30% до 36% в шамотных кирпичах, увеличенное количество тепловых ударов (с воздушным охлаждением) более чем в 25 раз (к обычным шамотным кирпичам такое требование не предъявляется), в центральной части регенераторов используются полусиликатные кирпичи, в верхней части шамотные кирпичи с содержанием Al2O3 ≥ 40%.
Работа коксовальной камеры характеризуется цикличностью, обычно при загрузке угля температура поверхности стенки печи падает до 500~600°C, а в конце коксования температура поверхности стенки печи снова поднимается до 1000~1100°C. Из-за огромной разницы температур, кладка коксовальной камеры будет генерировать большое тепловое напряжение, которое легко приведет к трещинам, рыхлой структуре и снижению прочности кладки и т.д. Поскольку она также подвергается давлению расширения угля при коксовании, сильному механическому истиранию и ударам при загрузке угля и проталкивании кокса, а также химической эрозии и осаждению угля и т.д., что приведет к большим повреждениям поверхности стен коксовальной камеры. Поэтому стены и дно коксовальной камеры должны быть построены из плотного динасового кирпича. Используя кладку из динасового кирпича, можно контролировать кажущуюся пористость до 16%~17%, что позволяет эффективно улучшить теплопроводность стен печи и увеличить производственную мощность. Для того чтобы сделать хорошее уплотнение, необходимо использовать фасонную кирпичную кладку. Обычно для большой коксовой печи используется более 400 видов кирпича, а то и более 1000 видов. На 60-дырчатую коксовую печь объемом 44,3 м3, высотой 5,5 м требуется около 17 000 тонн огнеупорных материалов. Современные крупные коксовые печи по кремниевому кирпичу предъявляют очень строгие требования, предпочтительные динасовые кирпичи требуют гладких, аккуратных углов, небольших допусков по размеру.
На обоих концах коксовальной камеры, потому что, когда дверь открыта, температура внезапно упадет с 1000°C до менее 500°C, что превысило предел 573°C для стабильности объема динасового кирпича, поэтому огнеупоры возле двери больше не могут быть использованы динасвого кирпича, но выбрать жаропрочные, термостойкие шамотные кирпичи, высокоглиноземистые кирпичи, силлиманитные кирпичи, кордиеритные кирпичи, красные кирпичи для строительства кладки. Место, который находится между огнеупорными кирпичами и оболочкой, заполняется теплоизолирующими материалами.
Камера сгорания состоит из трех частей: стены печи, под печи и крыши печи. Поскольку камера сгорания и коксовальная камера расположены друг между другом, стена камеры сгорания является общей с коксовальной камерой и должна быть построена с плотной кладкой, чтобы предотвратить выход газа. Боковая сторона стенки камеры сгорания в основном подвергается воздействию высокой температуры, солей, содержащихся в угле и газе, поэтому рабочий слой камеры сгорания должен быть выложен динасовым кирпичом, технические требования к которому такие же, как и к кирпичу, используемому в коксовальной камере. Крыша малой коксовой печи выполняется из шамотного кирпича, а крыша большой коксовой печи – из кварцевого кирпича. Вокруг отверстия для загрузки угля из-за больших колебаний температуры его строят из шамотного кирпича. В верхней части крыши добавляют слой наполнителя, а также последовательно кладут шамотный кирпич, теплоизоляционный диатомитовый кирпич, верхний слой также должен принимать меры по герметизации и гидроизоляции.
Больше о динасовых изделиях для коксовых печей, нажимайте кнопку!
Подробнее